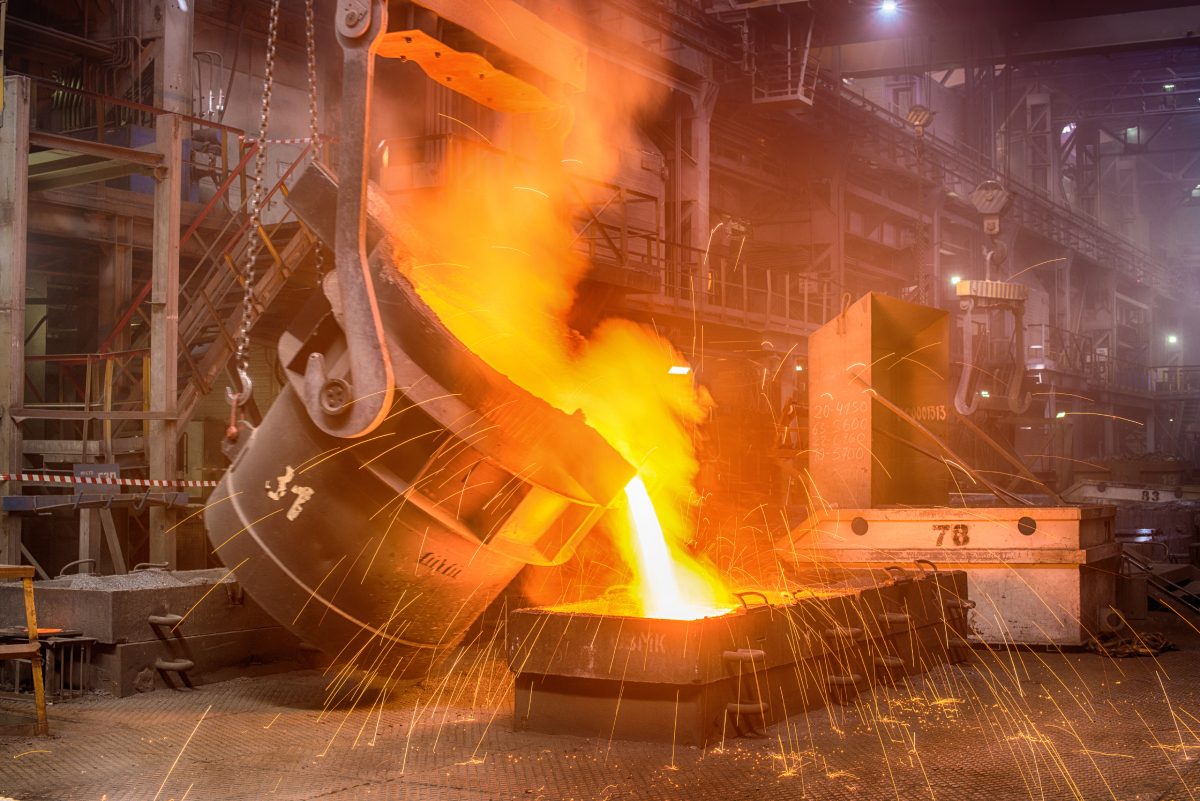
The Ultimate Guide to AOD Converter Setup: Key Components and Their Applications in Steel Plants
The AOD (Argon Oxygen Decarburization) converter is one of the most important pieces of equipment in modern steelmaking. It plays a pivotal role in refining molten steel, particularly in the production of high-quality stainless steel and special alloys. By reducing the carbon content in molten steel using a mixture of oxygen and argon, the AOD converter enables the precise control of chemical compositions required for specialized applications.
In this comprehensive guide, we will delve into the key components, setup considerations, and applications of AOD converters, providing insights into how they improve steel plant operations and product quality.
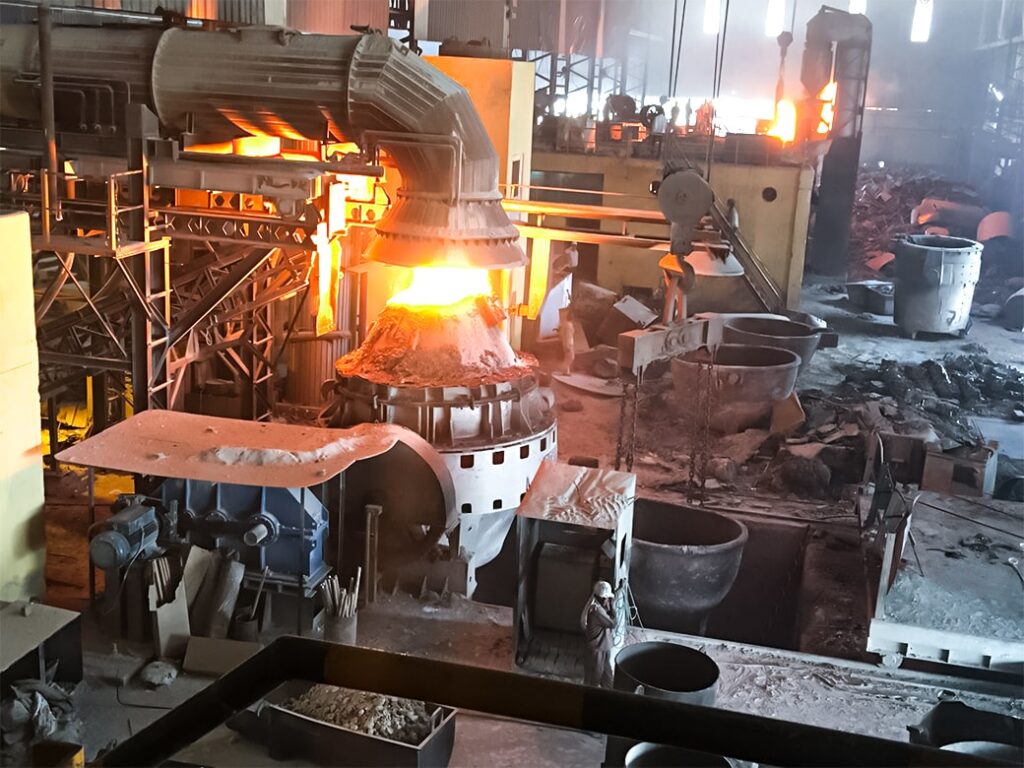
Key Components of AOD Converter Setup
An AOD converter consists of several critical components that work together to ensure efficient and controlled decarburization of molten steel. Understanding these components is essential for maintaining the longevity, efficiency, and reliability of the system.
Key Components:
- AOD Converter:
The main vessel where the decarburization process takes place. The converter is typically made of heat-resistant materials to withstand extreme temperatures. The interior is lined with a refractory material that helps maintain temperature and protect the structure of the vessel. - Trunnion Ring:
The trunnion ring supports the converter and allows it to rotate. This rotation is crucial for the proper mixing of gases and molten metal during the decarburization process. - Top Lance:
The top lance is used to inject the oxygen and argon gas mixture into the converter. This injection process is essential for lowering the carbon content of the molten steel and achieving the desired chemical composition. - Bull Gear and Gearbox:
The bull gear and gearbox are part of the converter’s drive system, enabling precise control of the converter’s rotation during the process. These components ensure smooth and efficient operation. - Tuyeres:
Tuyeres are nozzles through which the oxygen and argon gases are injected into the converter. These nozzles are strategically placed to optimize the reaction and promote efficient decarburization. - Hydraulic Tilting System:
The hydraulic tilting system allows the AOD converter to tilt, facilitating the pouring of the molten steel into ladles or other casting equipment. This system enhances operational flexibility and safety during the process. - Refractory Lining:
The refractory lining inside the AOD converter protects the vessel from the extreme heat generated during decarburization. The lining is made from materials like magnesia or chrome-based bricks that provide resistance to chemical wear and thermal shock.
Applications of AOD Converters in Steel Manufacturing
AOD converters are widely used in steel plants, especially in the production of stainless steel and specialty alloys. The versatility of the AOD process allows it to cater to various steelmaking needs, making it an essential tool for modern steel plants.
Applications:
- Stainless Steel Production:
The AOD converter is primarily used to produce stainless steel, which requires precise control over carbon, sulfur, and other impurities. By blowing a mixture of oxygen and argon into the molten steel, the AOD converter effectively reduces carbon content while maintaining the desired alloy composition. - Alloy Steel Production:
In addition to stainless steel, AOD converters are used in the production of alloy steels, which require specific amounts of carbon and other alloying elements like chromium, nickel, and molybdenum. The ability to fine-tune these elements makes AOD converters ideal for specialty alloys. - Refining of High-Carbon Steel:
AOD converters are also employed in the refining of high-carbon steels, reducing carbon content to create low-carbon or ultra-low-carbon steel. This is crucial for applications like automotive parts, machinery, and precision tools, where material strength and durability are paramount. - Production of High-Quality Steel for Critical Applications:
Industries such as aerospace, defense, and medical device manufacturing require high-quality steel with stringent chemical composition requirements. The AOD converter allows for precise control of these compositions, ensuring that the steel meets the rigorous standards of these industries.
Setup Considerations for AOD Converters
Proper setup and installation of AOD converters are crucial for ensuring their long-term performance and operational efficiency. Several factors must be considered during the setup process to achieve optimal results.
Key Considerations:
- Location and Space Requirements:
The AOD converter should be installed in a location that allows for easy access to other steel plant equipment, such as furnaces, ladles, and casting machines. Adequate space must be provided for the rotation of the converter and for the installation of necessary components like the hydraulic tilting system and the top lance. - Integration with Steel Plant Equipment:
The AOD converter must be integrated seamlessly with other steel plant equipment, including electric arc furnaces (EAFs), ladles, and casting machines. Proper coordination between these systems ensures that the entire production process operates smoothly and efficiently. - Automation and Control Systems:
Modern AOD converters are equipped with advanced automation and control systems that regulate the injection of gases, temperature, and chemical composition. These systems enable precise control over the decarburization process, enhancing both productivity and product quality. - Refractory Lining and Maintenance:
The refractory lining of the AOD converter should be periodically inspected and replaced as needed. Ensuring that the refractory lining remains intact is critical for maintaining the converter’s efficiency and longevity. Regular maintenance is required to avoid costly repairs and downtime. - Safety and Environmental Considerations:
AOD converters operate under extreme conditions, so safety protocols must be followed during installation and operation. Fume extraction systems and dust control measures should be implemented to safeguard workers and comply with environmental regulations.
Why Choose Ashutosh Engineers for AOD Converter Setup?
Ashutosh Engineers offers comprehensive solutions for AOD converter setup, ensuring that steel plants can operate with maximum efficiency and precision. Our expertise in steel plant equipment design and manufacturing allows us to deliver customized solutions that meet the unique needs of our clients.
Why Choose Ashutosh Engineers:
- Expertise in AOD Converter Design and Setup: With over two decades of experience, we specialize in designing and installing AOD converter systems that integrate seamlessly with other steelmaking equipment.
- Customization: We offer tailored solutions based on your plant’s capacity, production requirements, and specific steel products.
- Quality Assurance: Our products undergo rigorous quality checks to ensure they meet industry standards and provide reliable, long-lasting performance.
- Global Reach: We serve clients across the globe, providing turnkey solutions for AOD converter setup and maintenance.
Optimize your steel manufacturing process with Ashutosh Engineers’ AOD converter setup solutions. Contact us today to learn more about how our expertise and customized solutions can help you achieve higher efficiency, better quality, and reduced operational costs.